Why Checking References Is Essential for Subcontractor Prequalification
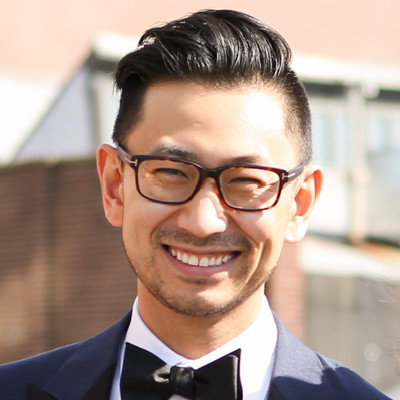
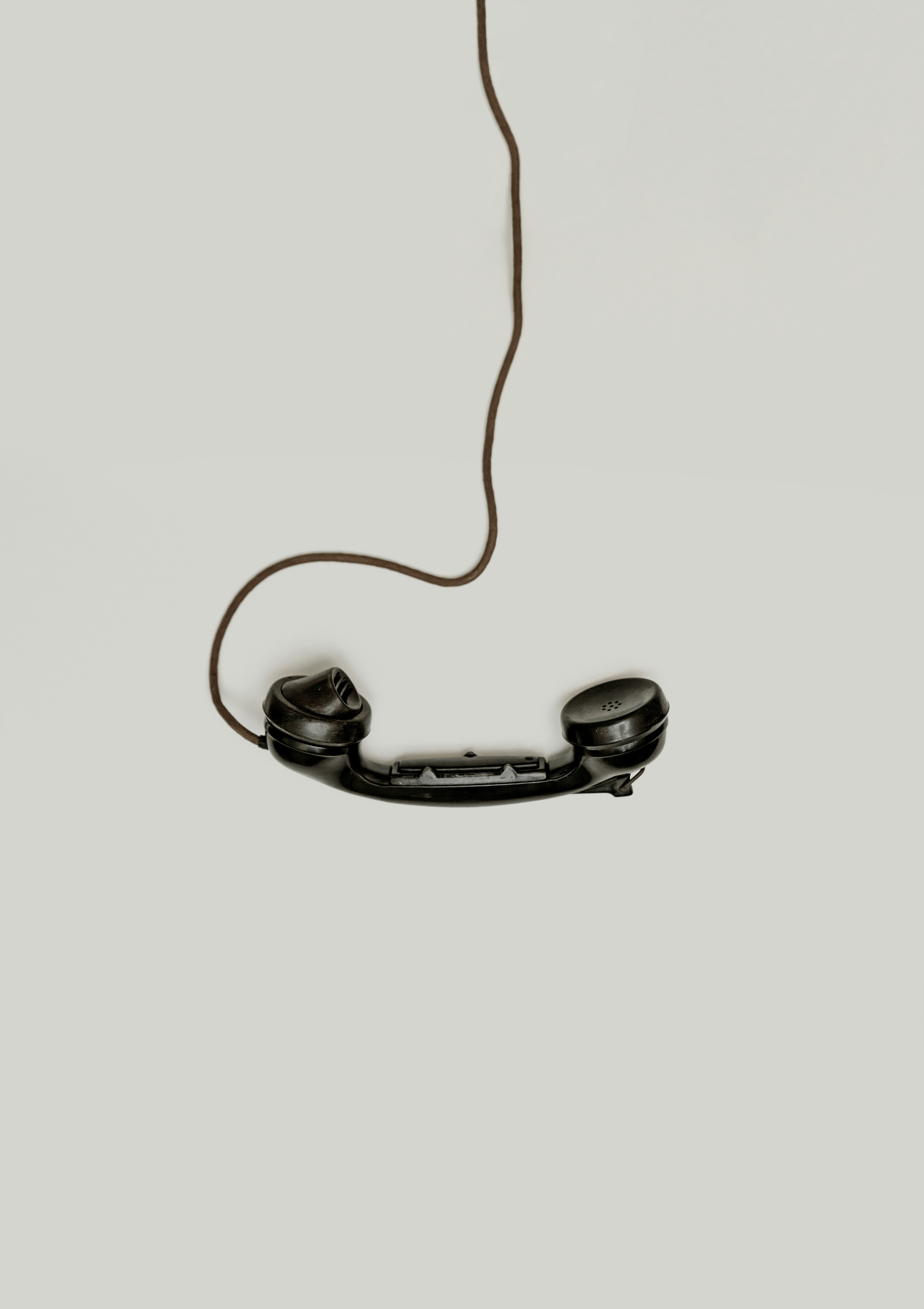
Most general contractors ask subcontractors and suppliers for three past project references as part of prequalification. But how many companies actually check all those references?
Past project references for subcontractors and suppliers are a key part of the prequalification process. They can ease your project's decisions, collaboration, quality, and costs. Plus, they can improve your brand's long-term growth. However, before you call a single reference, you should first understand why checking subcontractors' past performances is so important.
The Importance of Checking References for Subcontractors and Suppliers
It's not enough to simply trust that a subcontractor is legitimate because they worked for another general contractor. You must actually take the time to contact their references to verify that their services are high-quality and reliable. This is crucial for your project's budget, productivity, and subcontractor relationships.
Subcontractors' resumes may look impressive, but you must remember that they wrote those themselves. This means that many details could be exaggerated or fabricated. Of course, it's unlikely that a subcontractor or supplier would submit fake resumes and documents. Still, some subcontractors might cite past projects that they were removed from or did not perform correctly. You won’t know unless you check.
The Risks of Not Verifying References
Completing the prequalification process without checking references could put your project and integrity at risk. Subcontractors and suppliers who are prone to mistakes and delays will potentially bring their issues to your project. This could force you to repeat steps, put the work on hold, or potentially have to find a new subcontractor midway through the project.
Even if you've worked with a particular subcontractor before, you should still check their references — especially if time has passed. Management, teams, policies, and best practices can all change throughout the year. So, it's critical to do the leg work now and mitigate future risks.
What To Ask Subcontractors' and Suppliers' References
Be intentional with what you ask references to make the most of your brief conversations. Plan project-specific questions in advance, such as how well the subcontractor worked with a particular material or process. You should also leave space in your conversation for the reference to share their own thoughts. They may discuss advantages or disadvantages you hadn't even considered.
Your reference check questions may include:
- How well did the subcontractor communicate throughout the process?
- Did the subcontractor begin on their contracted start date?
- Were there any delays or setbacks, and were these reported?
- How did the subcontractor respond to setbacks?
- Were there any issues with the supplier's inventory or deliveries?
- How close were the final costs to the initial estimate or proposal?
- Would you recommend this subcontractor or supplier for a complex project?
Why Are General Contractors Not Collecting References?
Professional subcontractors provide their references and necessary contact information during the prequalification process. So why aren't general contractors doing anything with them? Every contractor is different, but this is often due to a lack of time and motivation.
In today's high-productivity market, spending hours preparing reference check questions and making calls may seem inefficient. Contractors with limited staff and manpower may not even have enough work hours in their week to do so. Plus, some contractors may not even see checking references as a priority. However, these contractors must remember that making these short calls could save them time in the future.
4 Benefits of Checking Past Project References for Subcontractors and Suppliers
Past project references for subcontractors are a crucial part of the prequalification process for many reasons. Below are the most significant benefits of checking references.
1. Improve Collaboration and Trust
Your operations team will need to know if they can genuinely rely on subcontractors and suppliers, especially with new contracts. Verifying subcontractors' qualifications based on past performances can improve trust and accountability with your construction employees. This way, instead of double-checking every fine detail, the operations team can jump into the collaboration process, knowing the project will be handled competently.
This level of relationship-building is also important for your business's long-term growth. Healthy subcontractor and supplier relationships with the general contractor may encourage them to work together again. As a result, you can keep high-quality subcontractors in your network and not have to worry about contacting multiple sources next time.
2. Keep Your Projects at the Industry Standard
One of the worst things you can do is complete a project with insufficient supplies or improper construction. Even if an error was caused by a supplier or subcontractor, it will still reflect solely on the general contractor.
Verifying your subs' past performances lets you confirm that their services meet the industry standard, at the very least. This is essential for protecting your brand and guaranteeing your finished construction projects look the way you want them to.
3. Avoid Profit Loss and Other Risks
Redoing steps, waiting for supplies, and other setbacks can be incredibly costly for your construction project. Even waiting an extra week for concrete can increase the costs of crews' wages and force other steps to be rushed. This is yet another reason to guarantee your subcontractors and suppliers have their business in order.
Of course, there are some risks you won't be able to avoid. For example, if you need a particular type of wood during a lumber shortage, even the best supplier may require additional time. Checking references and asking about past performances can also make you aware of the subcontractor's current processes and setbacks. This way, you can plan for risks cost-effectively.
4. Make Informed Decisions
General contractors should use as much information as possible when selecting subcontractors and suppliers. Compare each option's most significant advantages and disadvantages and consider which will serve your current project the best.
Checking subcontractors' references can drastically improve this decision-making process by giving you more tangible data. Plus, if you prepare project-specific questions, you can usually get answers that directly relate to your current goals.
Complete Your Prequalification Process by Checking and Automating References
Subcontractors' and suppliers' past project references are a key part of the vetting process. However, many general contractors lack the time and resources to actually write reference questions and make the calls.
With seamless automation and time-saving capabilities, Trestle Benchmark can simplify your prequalification process. Our software solution stores subcontractors' feedback and details and saves you time throughout your projects. Plus, its automation can provide the benefits of reference checks without you spending any time collecting them yourself. Schedule a demo with Trestle today to learn more.
Keep Reading
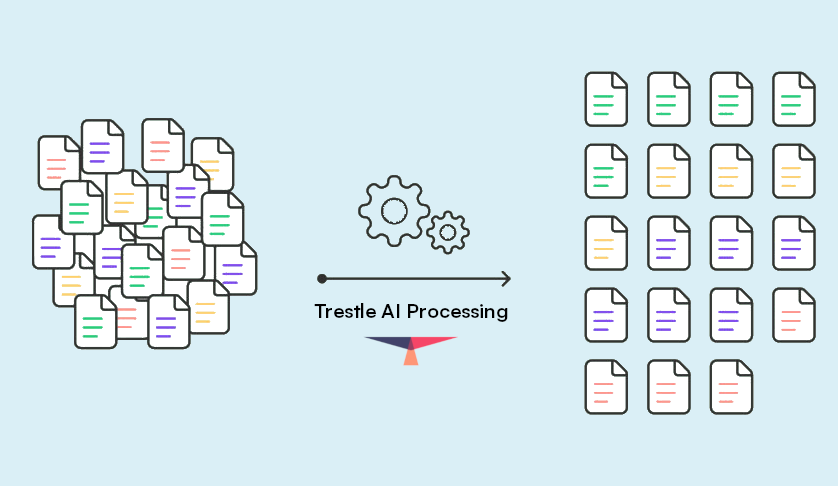
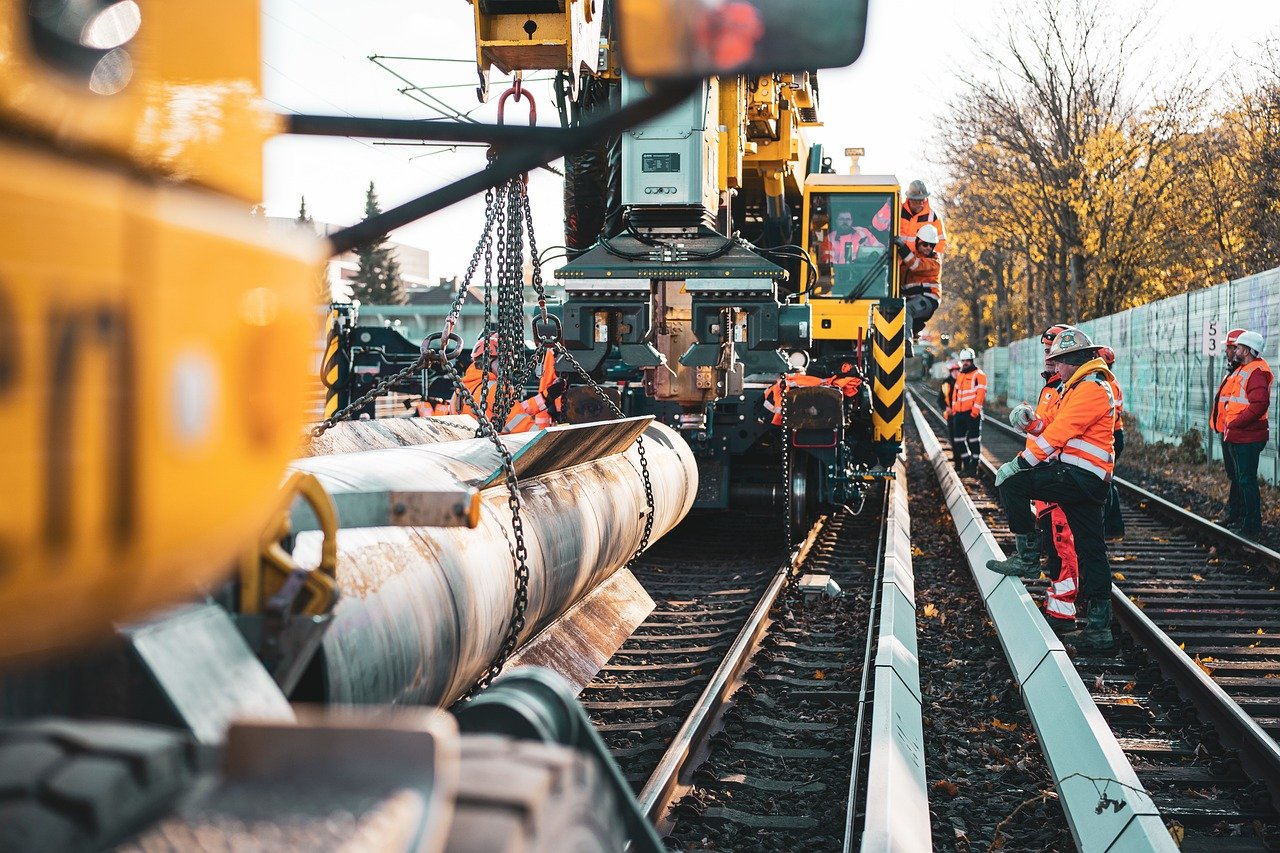
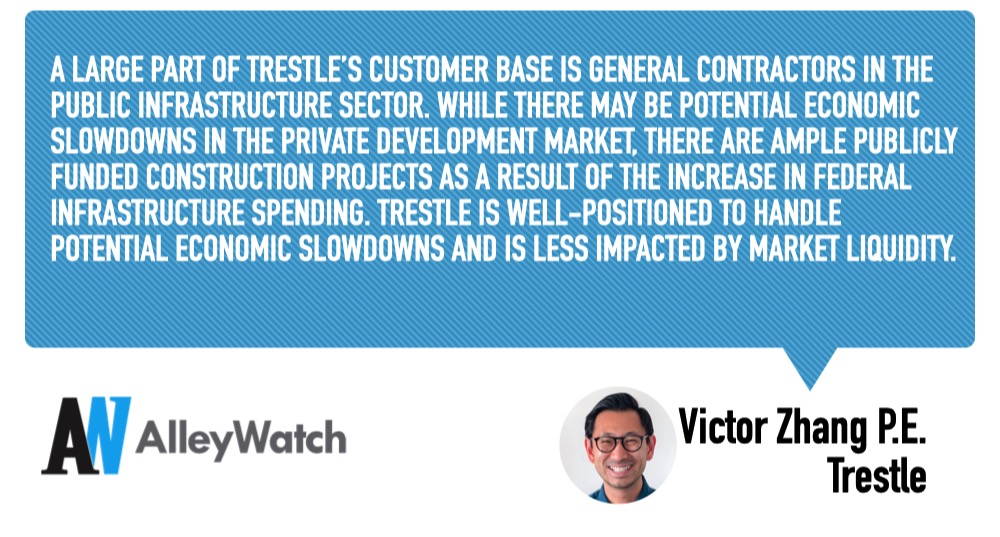